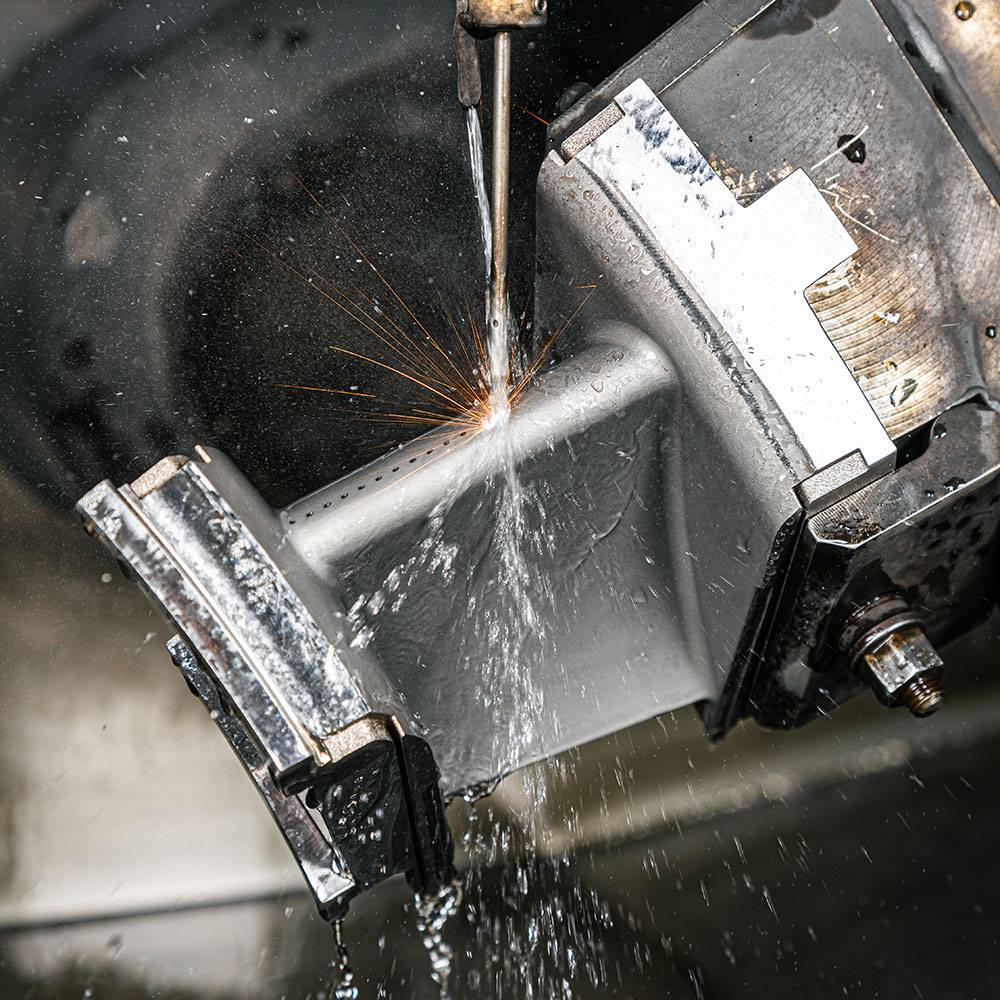
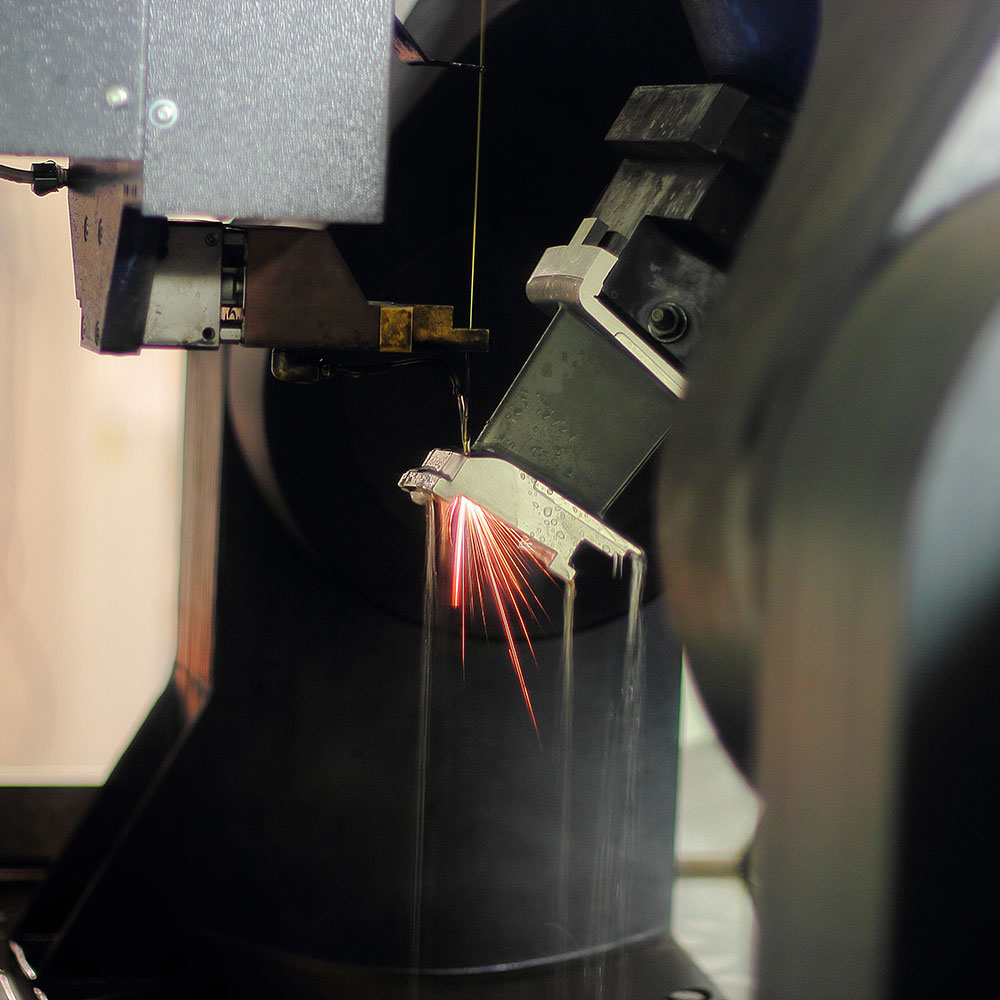
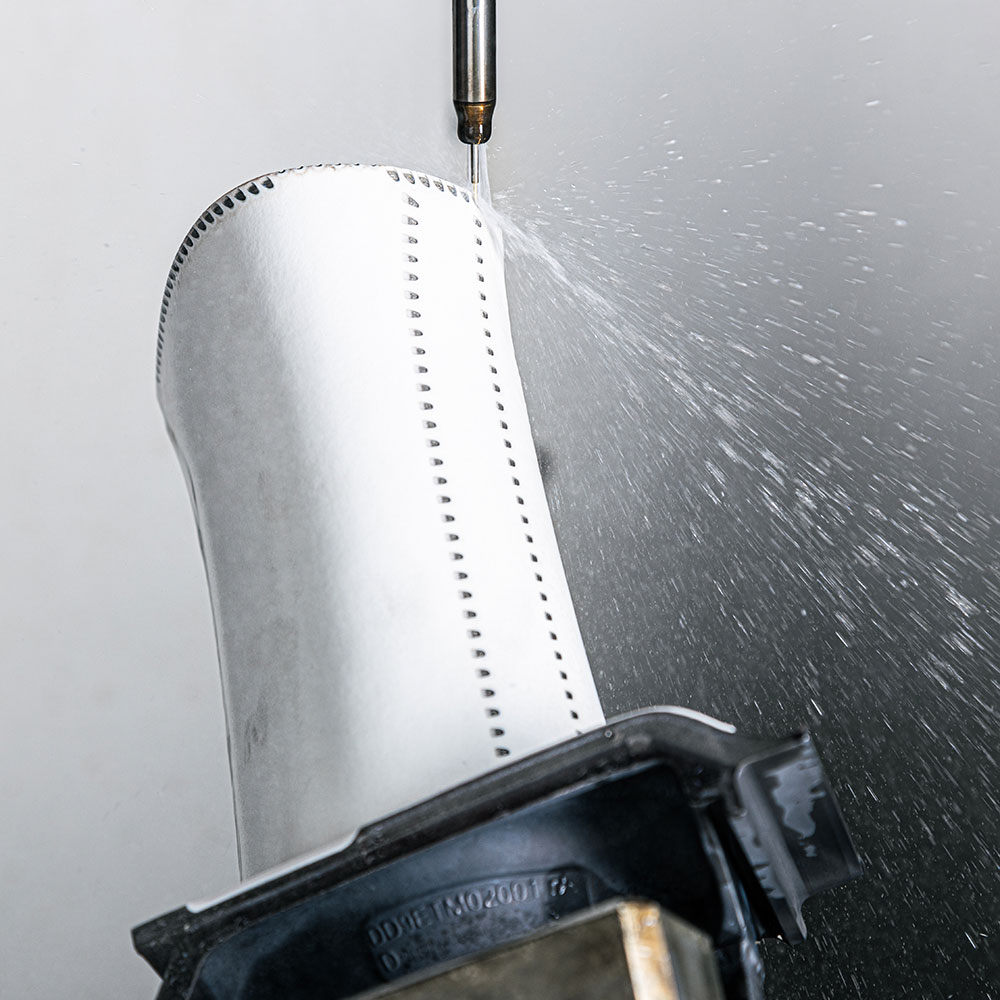
Technology
Fast Hole Drilling
Fast Hole Drilling (FHD) is a cost-effective method for producing small holes in hard, conductive materials to tight tolerances.
It’s an Electrical Discharge Machining (EDM) process which is ideal for producing holes greater than 0.3mm/0.012” diameter and up to 100m deep – and can also produce blind holes.
5-axis machining allows for easy access as well as fast and accurate location of hole positions. Our machines are developed for hole drilling of aero and industrial gas turbine blades, vanes and seal segments. The fast hole drill EDM machines feature are capable of generating shaped holes and have drill after coating (DAC) technology.
FHD is an alternative to the STEM drilling process, where depth to diameter ratio is not large. The process is also ideal when drilling holes on curved or angled surfaces as the electrode does not need to exert any pressure on the surface – making it perfect for machining holes on aerofoil surfaces.
ELE is also National Aerospace and Defence Contractors Accreditation Programme (NADCAP) approved for the EDM process.
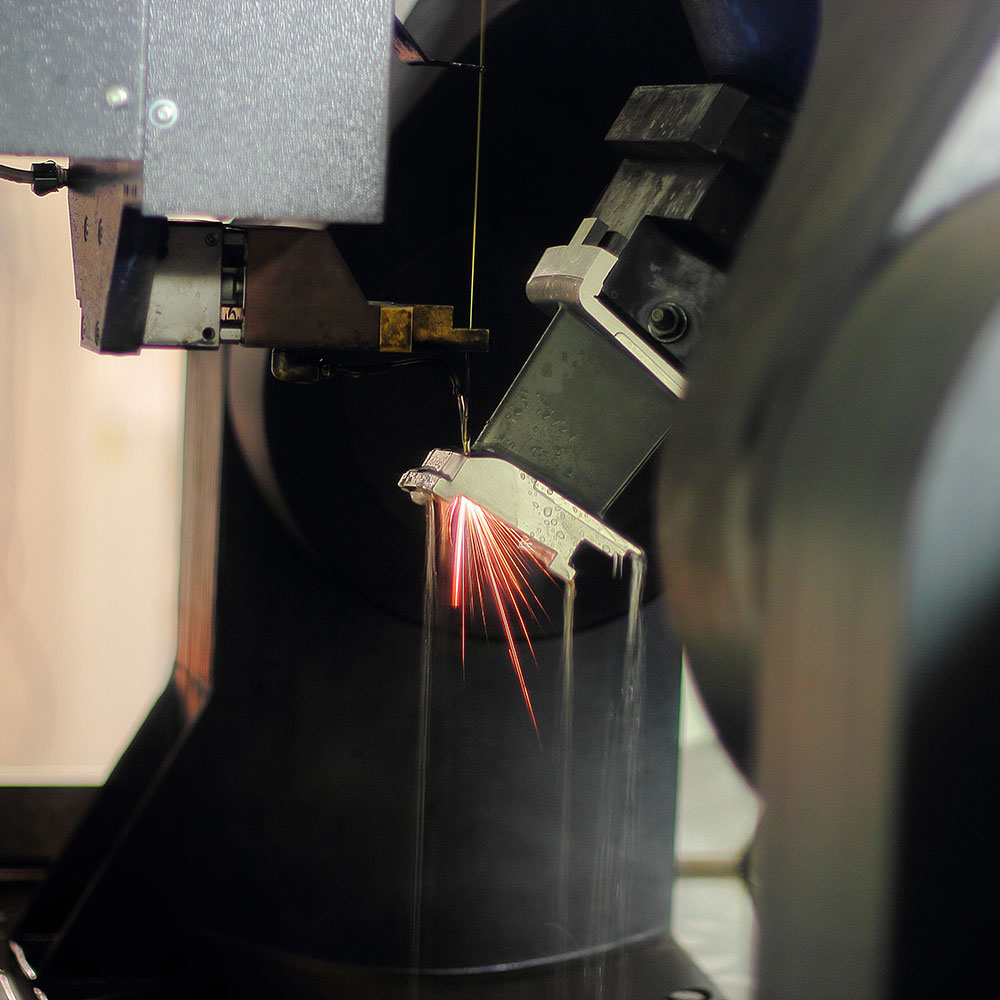
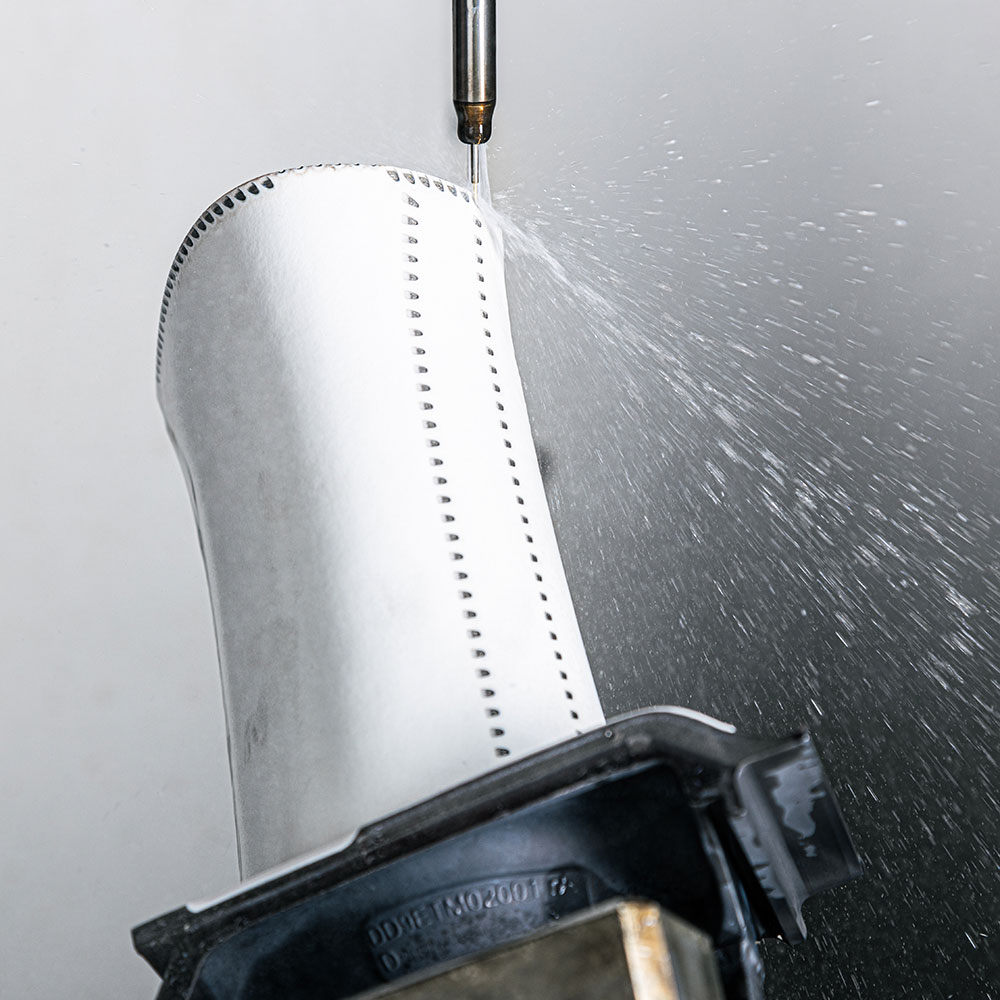